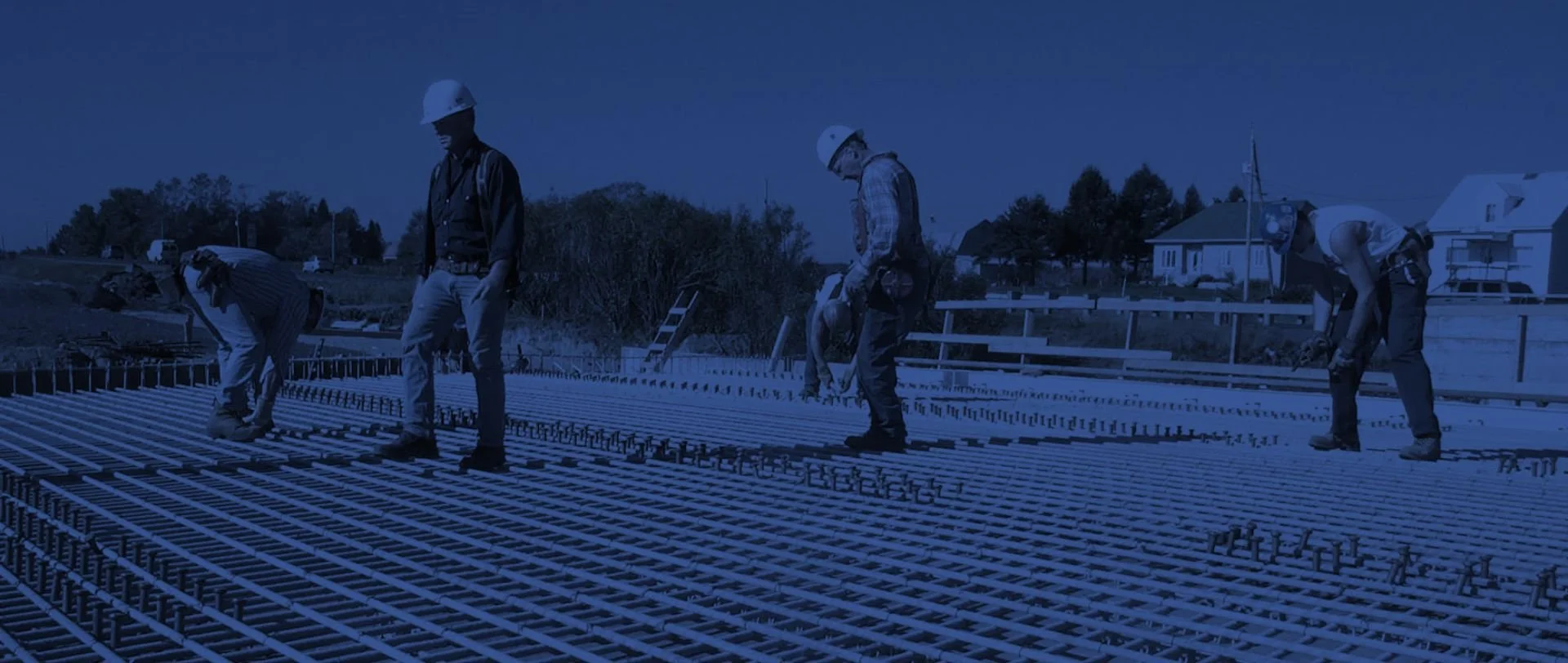
V-ROD Glass Fiber Concrete Reinforcement Bar
V-ROD is the reinforcing solution of the future. Trust in this sustainable rebar is shown by its qualification and presence in the main construction codes, as well as its adoption in the standards of authorities of many Canadian provinces, American states, and metropolitan cities around the world.
V-ROD Offers A Complete Range Of Composite Rebars
-
Lighter. Safer. Greener.
-
Available in multiple sizes and tensile strengths.
-
No corrosion. No thermal expansion. Magnetic Neutrality.
Applications
Want To Learn More?
Call (775) 245-3613 or email us at info@madewellconcreteproducts.com
The advantages of composite rebar in concrete structures
When safety and savings get along
The use of V-ROD fiberglass rebar provides significant savings while increasing users’ safety.
Savings on life cycle cost
Construction savings
Increased safety for owners and users
Green product
Corrosion resistance
Thermal insulation and lightness
Thermal expansion compatible with concrete
Electrical and magnetic neutrality
Superior tensile strength
Simplified management on site
Data Sheets
Consult the technical data sheets of our different products. Our experts will be happy to assist you in the selection and development of the best products for your projects.
Structural Glass Fiber Polymer (GFRP) Rebar
V-ROD 46 GPa
Structural
V-ROD 50 GPa
Structural
V-ROD 60 GPa
Structural
V-ROD Bent Bars 50 GPa
Structural
V-ROD Basalt 60 GPa
Structural
Nonstructural Glass Fiber Polymer (GFRP) Rebar
V-ROD Poly 40 GPa
Nonstructural
V-ROD Poly USA 46 GPa
Nonstructural
Book A Free Consultation
Our engineering team provides local assistance to infrastructure owners, engineers, contractors and fabricators.
Please fill out the form on the right and our team will be in touch with your shortly.
Alternatively, call us at (775) 245-3613 or email us at info@madewellconcreteproducts.com.